Navigating the Globe of Fasteners and Machining: Strategies for Accuracy and Rate
In the intricate world of fasteners and machining, the mission for accuracy and rate is a continuous difficulty that requires precise attention to information and critical preparation. From recognizing the varied selection of bolt kinds to choosing optimum products that can withstand rigorous needs, each action in the procedure plays an essential function in accomplishing the preferred result.
Understanding Fastener Types
When selecting bolts for a project, recognizing the various kinds available is vital for ensuring ideal efficiency and dependability. Screws are used with nuts to hold materials with each other, while screws are versatile bolts that can be used with or without a nut, depending on the application. Washing machines are crucial for dispersing the lots of the bolt and stopping damages to the material being secured.
Choosing the Right Products
Understanding the significance of choosing the appropriate materials is vital in making certain the optimal performance and dependability of the selected bolt kinds reviewed previously. When it comes to fasteners and machining applications, the material choice plays a crucial role in identifying the general stamina, toughness, deterioration resistance, and compatibility with the intended environment. Different materials offer varying buildings that can significantly impact the performance of the fasteners.
Common materials utilized for bolts include steel, stainless-steel, brass, aluminum, and titanium, each having its distinct strengths and weaknesses. Steel is renowned for its high strength and durability, making it suitable for a vast array of applications. Stainless-steel supplies superb deterioration resistance, suitable for atmospheres prone to moisture and chemicals. Aluminum is corrosion-resistant and light-weight, making it appropriate for applications where weight reduction is essential. Brass is typically chosen for its aesthetic allure and superb conductivity. Titanium is recognized for its phenomenal strength-to-weight proportion, making it perfect for high-performance applications. Selecting the appropriate product involves taking into consideration variables such as toughness demands, environmental conditions, and spending plan restrictions to guarantee the desired efficiency and durability of the fasteners.
Precision Machining Techniques

In addition to CNC machining, various other accuracy techniques like grinding, transforming, milling, and drilling play crucial functions in fastener manufacturing. Grinding aids accomplish great surface area finishes and limited dimensional resistances, while turning is commonly used to produce round components with exact sizes. Milling and drilling operations are crucial for shaping and producing openings in bolts, ensuring they satisfy precise requirements and function properly.
Enhancing Rate and Performance
To optimize fastener manufacturing procedures, it is necessary to improve procedures and apply efficient methods that enhance accuracy machining techniques. One essential method for boosting rate and efficiency is the implementation of lean manufacturing principles. By minimizing waste and concentrating on continual renovation, lean practices help enhance and get rid of bottlenecks process. Furthermore, buying automation innovations can dramatically enhance production speed. Automated systems can deal with repetitive tasks with precision and speed, enabling workers to concentrate on more complex and value-added activities. Adopting Just-In-Time (JIT) inventory management can also improve efficiency by guaranteeing that the best materials are available at the right time, minimizing excess supply and minimizing preparations. Fostering a culture of partnership and interaction among group participants can boost overall effectiveness by advertising transparency, problem-solving, and advancement. By incorporating these approaches, manufacturers can achieve an equilibrium between rate and accuracy, eventually improving their competitive side in the bolt industry.
Top Quality Control Actions
Implementing rigorous quality assurance actions is essential in ensuring the dependability and consistency of bolt items in the manufacturing process. Quality control procedures encompass different phases, starting from the option of raw products to the last inspection of the ended up fasteners. One fundamental aspect of quality assurance is carrying out extensive product assessments to confirm compliance with specifications. This involves evaluating elements such as product structure, toughness, and toughness to ensure that the bolts satisfy industry criteria. Furthermore, monitoring the machining refines is vital to maintain dimensional accuracy and surface finish quality. Using advanced innovation, such as automated assessment systems and precision measuring devices, can enhance the accuracy and performance of top quality control treatments.
Normal calibration of tools and machinery is essential to maintain uniformity in production and ensure that bolts meet the necessary resistances. Implementing rigorous protocols for recognizing and attending to defects or non-conformities is crucial in avoiding substandard products from entering the market. his comment is here By establishing a comprehensive quality assurance framework, producers can promote the credibility of their brand and deliver fasteners that satisfy the highest criteria of efficiency and toughness.
Verdict
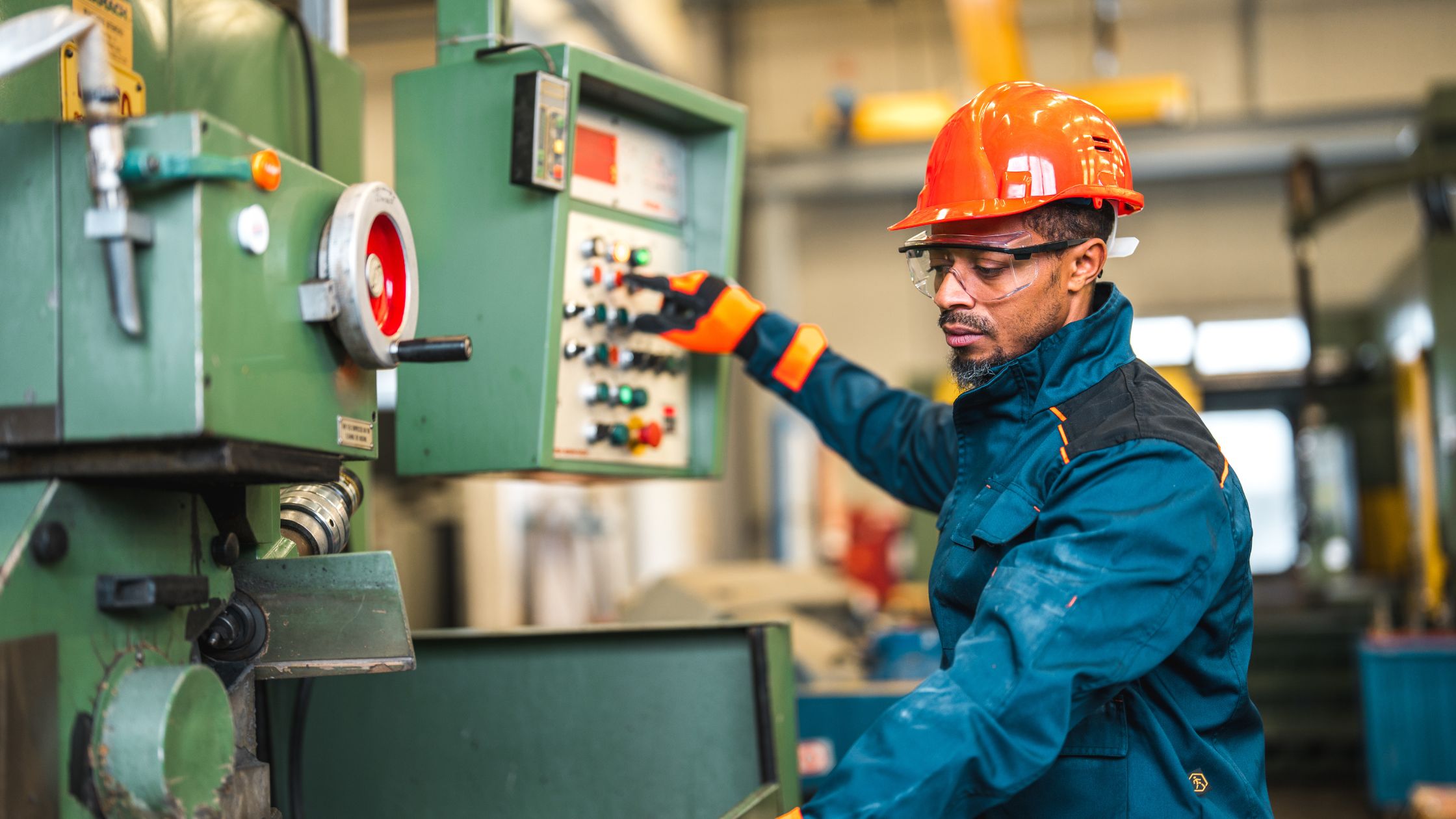
In the complex world of bolts and machining, the pursuit for precision and speed is a continuous challenge that demands meticulous attention to detail and calculated preparation. When it comes to bolts and machining applications, the product choice plays a crucial role in determining the total toughness, durability, rust resistance, and compatibility with the desired environment. Precision machining involves numerous advanced techniques that ensure the limited tolerances and specifications needed for bolts.In our website addition to CNC machining, other accuracy strategies like grinding, transforming, milling, and boring play essential duties in bolt manufacturing.To enhance fastener production procedures, it is vital to streamline operations visit their website and execute effective strategies that enhance accuracy machining strategies.